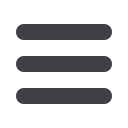
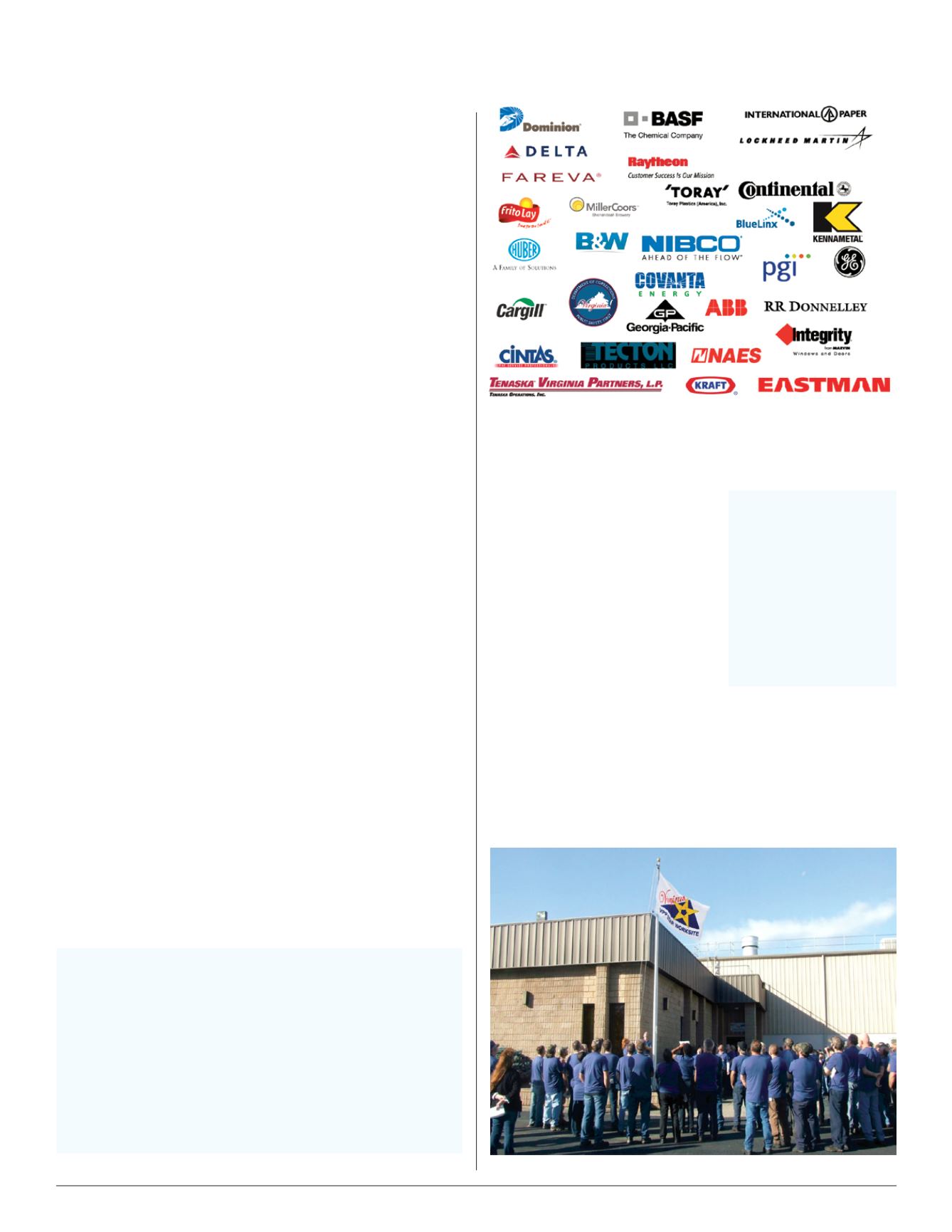
V
irginia
C
apitol
C
onnections
, W
inter
2015
12
Delta Airlines, Miller Coors, Raytheon, Eastman Kodak,
International Paper, Dominion Power and the Lunenburg Correctional
Center, are just a small sample of the 43Virginia employers providing
exceptional worksite safety and health protections for over 11,000
employees through the Virginia Department of Labor and Industry’s
(DOLI) Voluntary Protection Program (VPP).
Virginia VPP participating worksites average 65% lower injury
and illness rates than their counterparts in their respective industries.
With the average cost of a non-fatal workplace injury to an employer
of $53,000 (source: National Safety Council), the value of providing
workplace safety and health protections through VPP becomes self-
evident. But VPP is much more than just saving money. Virginia VPP
members report improved employee morale, and increased productivity
and competitiveness, to go along with decreased absenteeism, and
lower workers’ compensation costs and insurance premiums.
What is the
Voluntary Protection Program (VPP)?
VPP was originally created in 1982 by the US Department of
Labor’s Occupational Safety & Health Administration (OSHA) as a
voluntary partnership of employees, management and government
to recognize and promote occupational safety and health excellence.
VPP now engages approximately 900,000 employees at over 2,300
places of work in America.
In 1996, the Virginia Occupational Safety and Health (VOSH)
program adopted VPP as a component of DOLI’s larger mission to
“make Virginia a better place in which to work.” The Virginia VPP is
based on the national model with two levels of participation, STAR
and MERIT, and is currently restricted to fixed site locations.
Besides meeting all required VOSH safety and health standards,
each site that is considered must have rates of occupational injuries
and illnesses that are below their respective national rates and meet
the requirements of the four major elements of VPP:
• Management Leadership & Employee Involvement
• Worksite Analysis
• Hazard Prevention & Control
• Safety & Health Training
The VPP concept recognizes that enforcement alone can never
fully achieve the objectives of the OSH Act of 1970. Exceptional
safety and health management programs that go beyond VOSH
standards can protect workers more effectively than simply complying
with laws that set minimum safety requirements. Historically, VPP
sites average over fifty percent less OSHA recordable injuries and
experience dramatically lower workers’ compensation costs.
Beyond these facts, many VPP sites are ‘the “Best of the Best” in
numerous other measurable ways.
What does it take
to become a VPP participant?
An initial inquiry by an employer
to DOLI’s VPP Office starts a process
of self-evaluation for conformance
to the VPP elements, mentoring from
other VPP sites and corrective actions
as needed. A VPP application can
be completed once the annual self
evaluation finds a compliant safety and
health management system in place
and functioning. This process is self-
paced and requires documentation to
be provided to DOLI’s VPP division.
Once a VPP application is
accepted, a visit to the site is scheduled to observe the functioning
and documentation of the VPP safety and health management
system by VOSH VPP staff. Then a volunteer VPP Evaluation Team
conducts an onsite evaluation and a report is prepared to detail the
site’s efforts to conform to VPP elements, highlight the best practices
observed, and discuss recommendations to improve the effectiveness
of the applicant’s safety and health programs. After any deficiencies
are corrected, final approval is determined by DOLI’s Commissioner.
Virginia’s Voluntary Protection Program
...the Best of the Best!
NIBCO staff looks on during VPP Flag Raising Ceremony.
Some of the many VPP participants.
Cintas in Chester, Virginia, has received the Cintas Annual
Outstanding Achievement Award for the 6th time this past
year. Mr. Howard Baron, General Manager, states that
“VPP has provided our employees with many opportunities
to continuously improve performance and boost pride.”
The Chester site consistently achieves high national
rankings among 430 worksites in the Cintas Corporation
in the US and Canada. Additionally, the site has received
numerous awards for management leadership, sales and
profits results and has experienced very low turnover of the
site’s 122 employees.
One Virginia company
during its application
process saw its
total expenditures
on workers’
compensation claims
reduced as follows:
2008: $293,481.70
2009: $47,346.31
2010: $6,651.36
By Milford Stern, Jay Withrow, Bill Burge, Chris Buisset, Jim Morris